The manufacturing sector is a very strong and everlasting industry within the nations. We all need goods that have to be produced somehow and somewhere. In 2018, the annual value added to Gross Domestic Product (GDP) by the manufacturing industry represented 3.9 trillion USD for China, the biggest manufacturer in the world [1].
In the same year, the US added 2.32 trillion USD to their annual GDP, followed by Japan, Germany, South Korea, India, Italy, France, the UK, and Mexico to complete the top 10 of countries that most added to their GDP due to the manufacturing industry [1].
But, as everlasting as it can be, the manufacturing industry, like any other industry, can suffer ups and downs. As for 2020, the global COVID-19 outbreak caused a major decrease in manufacturing production.
The United Nations Industrial Development Organization (UNIDO) forecasted that at the end of the year, the global drop would be at 8.4 % due to national efforts to fight the pandemic that affected both demand and supply in the sector [2].
It’s been a tough year: in the second quarter of 2020, global manufacturing output decreased by 11.2 % less than the same period in 2019 [2].
Nevertheless, we’re talking about an unstoppable sector, where not all the markets have been equally affected: for example, the automotive industry was roughly hit and it’s understandable because cars weren’t a primary need in confinement.
But, precisely, plastic manufacturers have had a key role within the coronavirus crisis, since personal protective equipment (PPE) and many supplies for health care are made of plastics. Think about also in all the packaging for edible goods.
In the end, it appears that the manufacturing industry, in general, will regain its momentum with some sectors, such as plastics, being less affected. In this post, we’ll talk about some manufacturing processes for plastics and issues related to them.
Clearly, the plastic industry has been affected by the current situation: click here to find out how plastic manufacturing companies have been coping with the COVID-19 crisis.
Main manufacturing processes for plastics
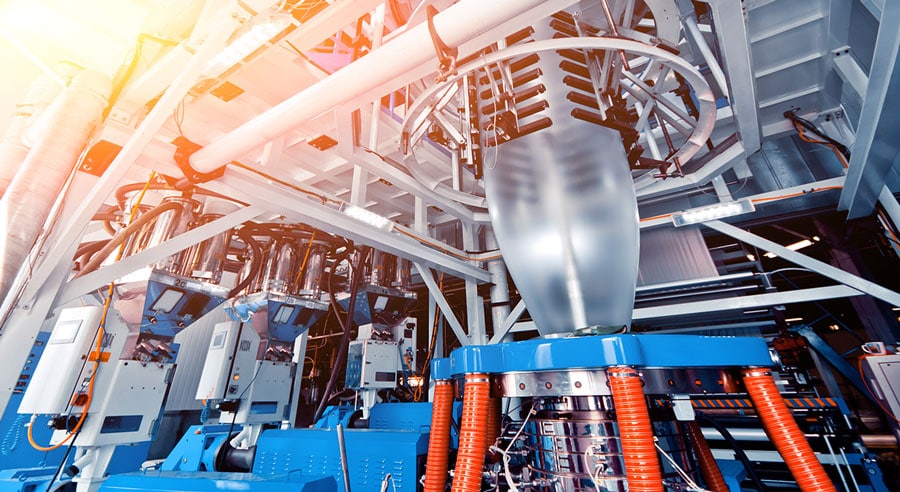
There is a good variety of different manufacturing processes for plastics. Choosing one of them depends upon the item you want to produce. Hollow goods would benefit more from extrusion blow molding, for example, than vacuum forming.
The form of the products, if it’s T-shaped, L-shaped, tubular, square, or circle, the complexity of them (are they made of one piece or many pieces?), and the amount required are also important variables to take into account.
Here, we’ll present to you some manufacturing processes for plastics that create practically every plastic piece or item that’s in your house, your workplace, or anywhere in everyday life.
Let’s just add something: it is important to stress that a step before producing some plastic goods consists of product designing. You can’t expect to have a good item if no one invests in making a prototype. Plastic product design has a key role in making good-quality merchandise.
Manufacturing companies, like Martin’s, may offer you an all-in-one service: we find solutions for product development and we present to our clients how their imagined product can exist. Message us to get in touch and start working with your project. Now, let’s get into the details about some of the current manufacturing processes for plastics.
Eager to learn about how some specific products are made?
Read here about toy factories and how these wonderful objects are done.
Plastic injection molding
By far, this is the most popular plastic manufacturing method. It works by injecting molten thermoplastics into a mold. Amongst the manufacturing processes for plastics, it’s one of the most complexes too due to the steps and pieces used, and it’s how virtually any product in Martin’s gets done.
The king of the manufacturing processes for plastics: it is estimated that about 80% of durable plastic items are made by plastic injection molding [3].
We can summarize the plastic injection molding process in four steps [4]:
- Mold setup: molds are essential for this process, so here they are placed and closed by a hydraulic press.
- Plastic extrusion: plastic pellets are melted and then extruded by a screw and through a hot chamber.
- Molding: once molten, the liquified plastic is injected into the mold and fills the cavities.
- Cooling: the piece cools inside the mold until it solidifies and then it’s released, either by compressed air or mechanically.
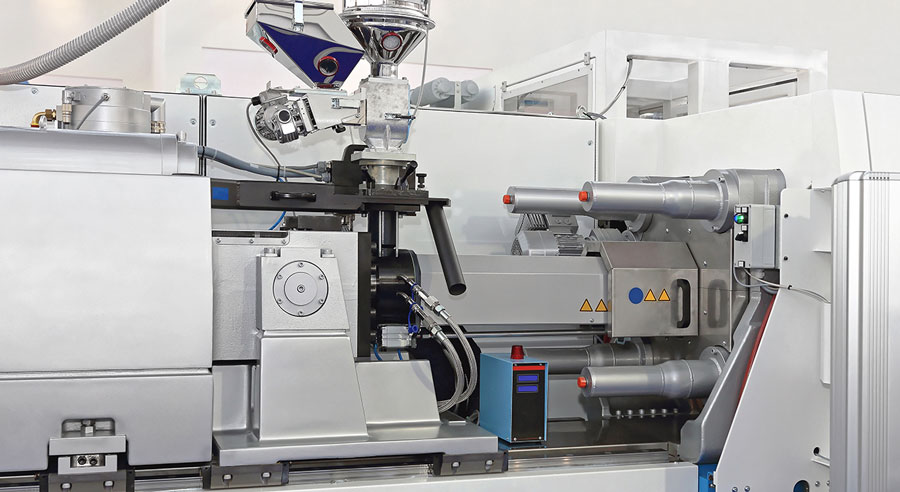
Molds for this method are very complex and they need excellent manufacturing to produce high-quality pieces. In Martin’s, we use top-notch techniques regarding molds and tools. Our tool fabric in Hong Kong has automatized machines.
The insertion of molds is supervised by specialized engineers and highly-skilled and trained staff before they start to produce in our plants. In Martin’s, we offer a variety of injection molding techniques, from hot and cold runners to two-parts molds, depending on the required product.
A total of 29 plastic injection molding machines, distributed in our three plants in Mexico City, give Martin’s the capacity to produce great amounts of plastic goods. Lastly, plastic injection molding is a fast process and it’s used to manufacture large numbers of identical pieces, from high-precision engineering components to a wide variety of consumer goods [5].
If you already have a project in mind and are eager to invest in good-quality plastic products, in Martin’s, we are sure we can be of help. Reach to us and we’ll offer you the best assistance.
Rotational molding
Similar to plastic injection molding, rotational molding also uses molds, but the manufacturing process is not the same. This is an ideal method for large, hollow, and concave shapes [3].
In this method, liquified plastic is added to the mold from the inside and so it forms the object. Two mechanical arms or axes hold the mold in place. While the plastic is being added, the axes spin constantly, to make the mold rotate [6].
As the mold turns, the plastic coats the inside of that mold. As a result, a new hollow plastic object is created. Rotomolding is ideal for short-run production, as it has a long time cycle since the entire mold must be heated and cooled [4].
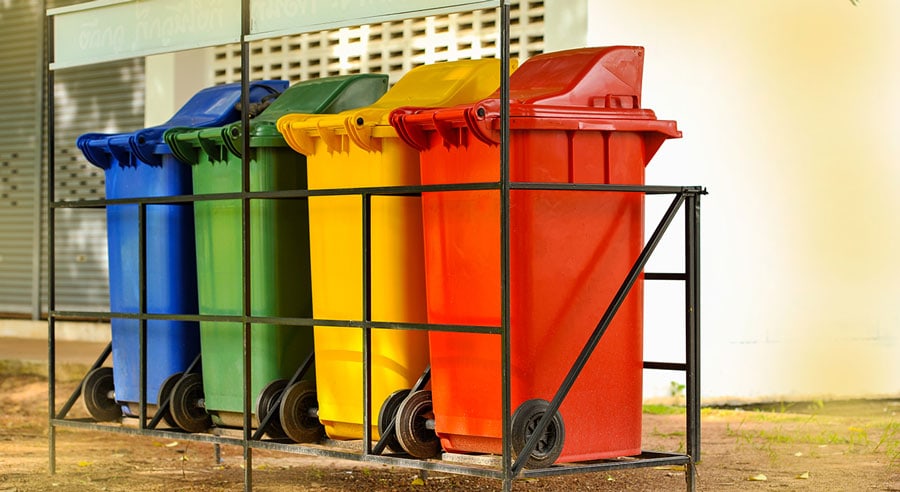
bollards, automotive parts, kayaks, canoes, and boats.
Extrusion blow molding
In the manufacturing processes for plastics, extrusion molding is also a common method, similar to injection molding and used to make pipes, tubes, straws, hoses, and other hollow pieces.
A fast method and with readily produced tools, the downside of extrusion blow molding is that the parts cannot be very complex or high-precision made [3].
The plastic resin is placed into a barrel where it is liquified. Then, a rotating screw drives the liquid plastic into a mold with a tube-shaped orifice, the size and shape of it will depend on the size of the piece required [6].
Compressed air then is blown to fill the mold. The plastic then cools and is fed through an extruder. The extruder flattens the plastic and it gives the final shape for the product. Due to the simple shapes, the molds are less expensive than the ones for injection molding [4].
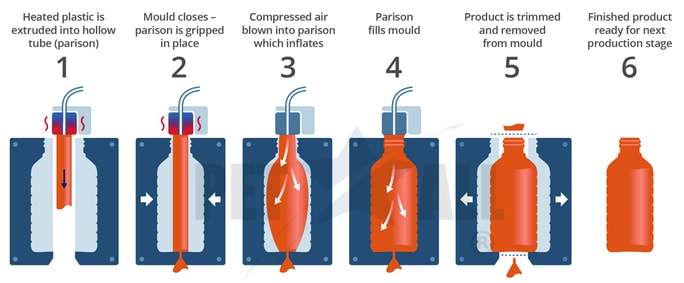
such as bottles and other liquid containers. Source: Pet All Manufacturing.
Other manufacturing processes for plastics
As we’ve mentioned, there are a lot of different manufacturing processes for plastics. Some of them differ very little, but others can be very dissimilar. Here we introduce to you other three methods, followed by a brief description of them:
1. Injection Blow Molding:
Not to be confused with plastic injection molding; injection blow molding is used specially for production of hollow objects in large quantities. The main applications are bottles, jars, and other similar containers [5].
During injection blow molding, gas pressure propels the molten resin into a mold cavity. The whole process is easily managed, thus repeatable, being a good method for big productions [3].
2. Vacuum Forming:
Vacuum forming is the most common type of thermoforming, which is, in turn, one of the oldest manufacturing processes for plastics. Many vacuum formed products, such as pieces of appliances, play a major part in everyday life.
In short, the process involves getting a plastic sheet heated until it is soft and then covering a mold with it. A vacuum sucks the sheet into the mold and then it is ejected [5].
In its advanced form, the vacuum forming process uses high technology pneumatic, heat, and hydraulic controls. These tools enable higher production speeds and more detailed vacuum formed applications [5].
3. 3D Printing:
One of the most recent types of manufacturing processes for plastics, 3D printing is still not advised for big-scale production. The process can be summed up in three steps:
First, the print setup, where the software is used to model the final product and add the details. Then, printing, which depends on the type of technology, but usually molten plastic is cured by stereolithography (SLA) and then fused by selective laser sintering (SLS). Lastly, post-processing involves removing, cleaning, or washing parts [4].
If you want to learn more about plastic fabrication and how the processes happen in a company, click here to get more detailed info.
Materials in manufacturing processes for plastics
Plastics are made of combinations of natural, organic materials, such as cellulose, coal, natural gas, salt, and most famous, crude oil through polymerization or polycondensation processes [7].
There are two main types of supplies to make plastic goods: thermoplastics and thermosets aka thermosetting plastics [4].
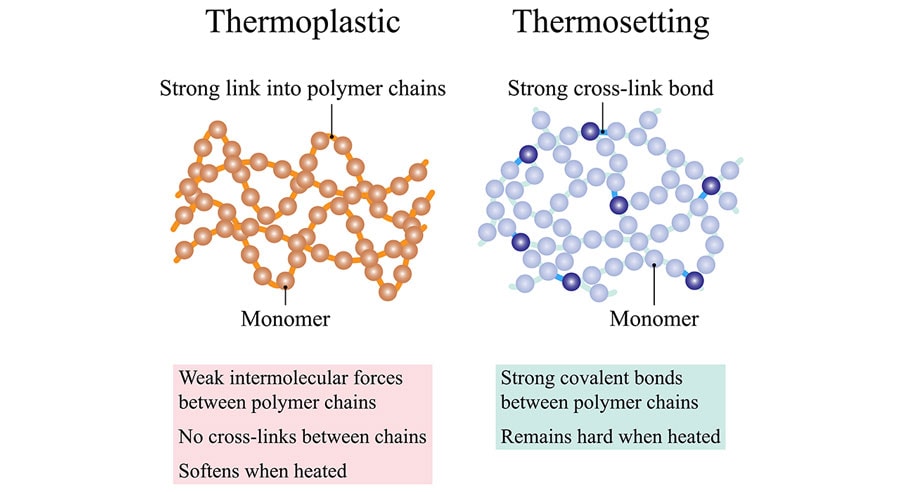
Thermoplastics are the most used type of plastic. The big difference with thermosets is their ability to go through many melt and cure cycles without major degradation. Thermoplastics are usually supplied in the form of small pellets or sheets [4].
Since the process is completely reversible because no chemical bonding occurs, recycling is feasible, that’s why this kind of plastic is an excellent option for manufacturing processes for plastic products.
Examples of thermoplastics include acrylic (PMMA), acrylonitrile butadiene styrene (ABS), polyamide (PA), polylactic acid (PLA), polycarbonate (PC), polyether ether ketone (PEEK), polyethylene (PE), polystyrene (PS), polypropylene (PP), polyvinyl chloride (PVC), thermoplastic rubber (TPR), and copolyesters.
Thermosetting plastics, by contrast, remain in a permanent solid state after they solidify. Polymers in thermosets get tied together during the curing process, induced by heat, light, or radiation. Accordingly, an irreversible chemical bond is formed. Recycling or reversing the process isn’t possible [4].
The most common thermosets are: cyanate ester, epoxy, polyester, polyurethane, silicone, styrene-butadiene rubber (SBR), and vulcanized rubber.
All of these materials are the foundation for an impressive amount of plastic goods, from appliances or clothing to toys or auto parts. Custom promotional products are also made from these supplies: click here to learn more about them.
In Martin’s, we use mostly thermoplastics like PP, PS, Tritan, a branded copolyester, TPR and with some products, we use Styrolyx, a brand of SBR. Do you want to manufacture plastic products on a big-scale? Click here to get in touch and we’ll gladly assist you.
Manufacturing processes for plastics: finishing and painting
After the product has been correctly created, we’re close to starting its trading. Finishing refers to different kinds of processes that intend to alter the surface of manufactured parts to achieve the desired appearance or provide durability [8].
The correct finishing processes are chosen based on costs, part specifications, and of, course, design.
Finishing processes aren’t exclusive for plastics, metal and wood made products can also go through their own finishing processes. As for plastics, painting is a common type of finishing. Here are some of the most popular ways to get a shiny, colorful and unique plastic product, easily explained [8]:
• Silk screening: aka screen printing or serigraphy, it involves ink that is transferred directly from a silkscreen (hence the name!) into the plastic piece.
• Heat transfering: also called heat transfer, it is a process where a heat transferable label or marking is applied to a plastic piece through heat and pressure.
• Hot stamping: during this process, a hot metal stamping die gets pushed into the plastic piece to leave a marking in the shape of the die.
• Engraving and etching: both processes mark the plastic piece, engraving does it with a laser or computer numerical control (CNC), while etching uses chemicals.
• Pad printing: aka tampography, it is similar to heat transferring and silk screening, but this method uses pads that get inked from etching and then push the design onto the plastic piece.
• Coating: this process requires a UV powder that gets applied to the surface of the plastic piece by electrostatics and then it’s cured with UV light.
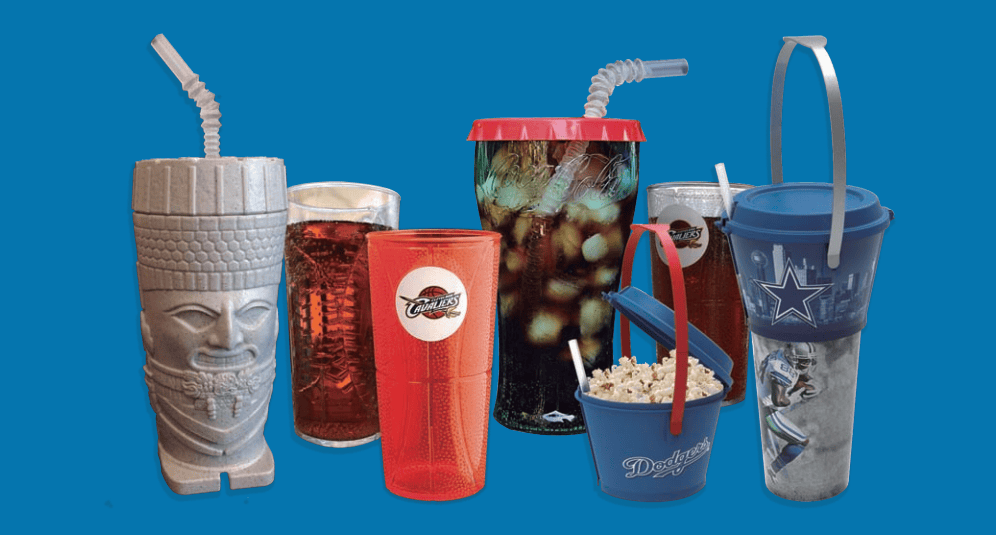
In Martin’s, we use different techniques: heat transferring, silk screening, pad printing, and the in-mold method. In-mold is a labeling technique that uses an adhesive sensible to heating and gets the plastic piece decorated during its manufacturing.
We would like to show to you our complete catalog which includes a wide variety of plastic products, houseware, drinkware, and promotional goods. Click here and see for yourself our high-quality work.
Steps beyond the manufacturing processes for plastics: assembly and packaging
Sometimes, plastic products are made of different pieces, so they will need to be assembled. There are a few different options to attach the pieces, for instance: traditional hardware, a chemical bonding agent, or ultrasonic welding [8].
Packaging is one big step before the product can be circulated to start selling it. In Martin’s, our most popular packaging options include blister pack, flow packing, and thermoforming packaging.
As we’ve said, Martin’s offers an all-in-one service, accordingly, we have different warehouses to store your final products and we also manage a distribution network that includes connections in Asia, Europe and through the Americas, we have different plants and commercial offices distributed in these regions.
In short, in Martin’s we help you from the very first step to the end. We’ll get you ready to start selling your product, the success will depend too upon your strategy: your facilities, partners, what about some retail marketing?
Are you eager to invest in that, but you don’t know where to start? Then a digital marketing agency is your best choice. As for your product, in Martin’s, we got you covered.
In the beginning, we mentioned the great impact the COVID-19 pandemic has had all over the world, but plastics are still a strong industry. Increasing plastic consumption in automotive, electrical, construction and electronics industries, as well as medical equipment and packaging is projected to drive the market for plastic in the next years [9].
In 2019, the global plastic market size was worth almost 569 billion USD. It was expected to grow at a compound annual growth rate of 3.2% from 2020 to 2027 [9].
In Martin’s, we’ll answer your questions concerning manufacturing processes for plastics applied particularly to your desired production. We’re ready to help you from the very conception of the idea to your product on shelves. Contact us to begin working together!
REFERENCES:
[1] Erin Duffin. Value added to GDP by the manufacturing industry for leading countries in 2018. Statista, 2020. Accessed 17 Oct 2020.
[2] UNIDO. World Manufacturing Production. Statistics for Quarter II 2020. United Nations Industrial Development Organization (UNIDO), 2020. Accessed 17 Oct 2020.
[3] Star Rapid. The Top 7 Ways of Forming Plastics. Star Rapid, n.d. Accessed 17 Oct 2020.
[4] Formlabs. Guide to Manufacturing Processes for Plastics. Formlabs, n.d. Accessed 17 Oct 2020.
[5] BPF. Plastic Processes. British Plastics Federation (BFF), n.d. Accessed 17 Oct 2020.
[6] Contributor. The Plastic Manufacturing Process. Sciencing, 2018. Accessed 17 Oct 2020.
[7] PlasticsEurope. How plastics are made. PlasticEurope, n.d. Accessed 17 Oct 2020.
[8] Synectic. The Final Step In The Product Development Process: Finishing and Painting Explained. Synectic, 2020. Accessed 17 Oct 2020.
[9] Grand View Research. Plastics Market Size, Share & Trends Report, 2020-2027. Grand View Research, 2020. Accessed 17 Oct 2020.
Leave a Reply