Entrar en el mundo de la fabricación de productos de plástico puede ser una tarea compleja. Las preguntas comunes son: ¿qué se puede hacer? ¿cuánto cuesta? ¿qué necesito para crear mi producto? Todas estas dudas son fáciles de resolver si conocemos el proceso general de inyección de plástico, así como la manera en que se cotiza un proyecto.
En esta guía comprenderás en qué consiste el proceso de inyección de plástico y cuáles son sus etapas más importantes y subprocesos. En la segunda sección haremos un recuento de cuáles son los productos más populares en la inyección de plástico con fines promocionales o lúdicos (juegos y juguetes), así como los procesos que intervienen comúnmente en su creación. En la última sección de esta guía profundizaremos en los costos y la viabilidad de los proyectos. Si ya tienes una idea de presupuestos y números, te ayudará a darte una idea del costo final de tu producto.
TABLA DE CONTENIDO:
Proceso de inyección de plástico: qué es y cómo funciona
El moldeo por inyección de plástico es uno de los procesos más comunes para la producción de cualquier producto de plástico. Consiste en inyectar material fundido en moldes especiales a la medida que dan forma y tamaño a la pieza.
Aquí termina realmente el proceso completo de inyección de plástico, pero para que el producto alcance su versión final debe pasar por diferentes etapas de producción secundarias. Muchos se refieren a la suma de todos estos procesos como inyección de plástico, a pesar de que es sólo la etapa primaria de producción.
Antes de pasar a los procesos secundarios, comprendamos la inyección de plástico en su totalidad.
Inyección de plástico
La maquinaria que se usa en el proceso de inyección depende mucho del tamaño de la pieza a fabricar. No es lo mismo crear un producto de unos gramos a uno de 4 o 5 kilos, lo que representa una diferencia importante de costos tanto en material como en producción. Sin embargo, el proceso de fabricación es muy similar.
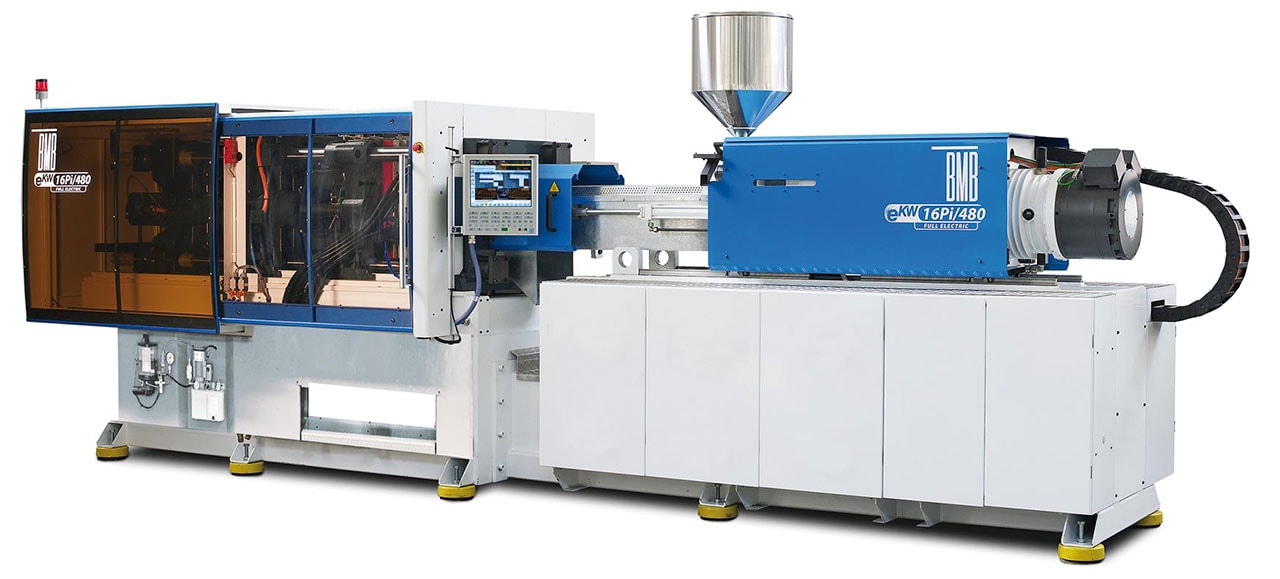
Todo comienza con la inserción de la materia prima a la maquinaria. El plástico sólido es transportado a través de la unidad inyectora donde se funde para convertirse en líquido.
Una vez que está completamente fundida, la materia líquida se inyecta en un molde, normalmente de 2 partes, montado en la unidad porta moldes. El líquido se enfría y da forma a la nueva pieza. Por último, la unidad desmoldadora separa las partes del molde y el producto es liberado.
Ya terminado el proceso, el molde vuelve a su posición original y se vuelve a inyectar material líquido para generar una nueva pieza. Así comienza la línea de producción.
Es importante considerar dos tipos diferentes de sistemas de moldeo de plástico, también conocidos como tipos de colada, ya que esto afectará el costo final del proyecto.
Cold runner
Una colada o sistema de moldeo es el camino que debe recorrer el plástico fundido para llenar la cavidad del molde y así dar forma a la pieza. En el cold runner o colada en frío, el material líquido debe recorrer todo un canal para llegar al centro del molde.
Este proceso genera cierto desperdicio de material y aumenta el tiempo en la producción, sin embargo es más económico de usar y mantener.
Hot runner
En el hot runner o colada caliente, el sistema dirige el material fundido por boquillas especiales que conducen directamente a las cavidades del molde. En la colada caliente, no existe tiempo de solidificación, desperdicio de material y se tiene mayor control sobre el llenado de cavidades.
El hot runner es más costoso, sin embargo los tiempos de producción son más veloces y el desperdicio de material es mucho menor.
Una vez entendidos los diferentes sistemas de moldeo, podemos pasar a los moldes, que son parte importante del proceso de inyección, pero también del primer proceso secundario del que hablaremos: el ensamblado.
Ensamblado
Durante el ensamblado, las piezas plásticas se unen y dan forma a una nueva pieza más compleja. Algunos procesos de ensamblado están relacionados directamente con los moldes, que también son importantes en el entendimiento y cotización de un proyecto.
Moldes
Dependiendo de la figura que se produzca y del tipo de ensamblado requerido, existen diferentes tipos de moldes. El molde convencional consta de dos partes, que después de la inyección y el enfriamiento se separan y dan lugar a la pieza. Sin embargo, si la figura es más compleja, es posible que necesite moldes con direccionamientos laterales o side actions.
Este tipo de molde se compone de varios segmentos, algunos laterales, que permiten que el proceso de desmolde sea más sencillo y la figura no se atore. En otro tipo de piezas, como las taparroscas, el mismo molde necesita mecanismos de desmolde dentro del mismo para hacer más sencilla la liberación.
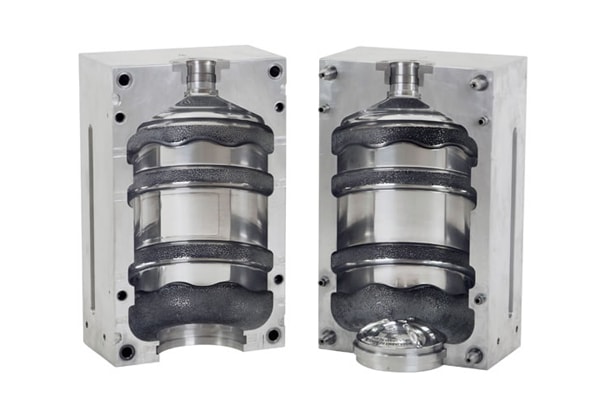
Tipos de ensamblado
El producto final definirá el tipo de ensamblado, si es que este es necesario. Existen diferentes tipos según el presupuesto del proyecto y el acabado de la pieza: ensambles mecánicos, sellado por ultrasonido y por medio de adhesivos.
Ensamble mecánico
Los ensambles mecánicos se planean mucho antes de la misma inyección de plástico. En su diseño se incluyen elementos que embonan entre las piezas, por lo que una vez sacados del molde, sólo deben embonarse a presión para su ensamblado final.
El ensamble mecánico ahorra material y esfuerzo en procesos extra, pero no funciona para todos los productos.
Sellado ultrasónico
El sellado por ultrasonido ocupa ondas ultrasónicas para derretir los poros del plástico y lograr la fusión entre ambas piezas. Así, las piezas plásticas quedan completamente unidas y ensambladas.
Adhesivos
Los medios adhesivos se limitan a diferentes tipos de pegamento para unir las piezas. Se pueden utilizar diferentes sustancias dependiendo del tipo de producto y el grado de adhesión necesaria.
La fabricación de muchos productos terminan en la etapa de inyección de plástico o en el ensamblado, pero si el producto necesita algún tipo de diseño, grabado o estampado, pasa al proceso de decorado.
Decorado
El decorado es un proceso secundario en el cual una pieza es pintada o estampada tras el proceso de inyección o ensamblado. Existen diferentes maneras de decorar un producto, dependiendo de la forma del mismo y del acabado final deseado.
Tampografía
Para los productos cilíndricos o de superficies irregulares, la tampografía es una de las mejores opciones. En este proceso un tampón de silicón recoge la tinta se coloca sobre la superficie e imprime los colores sobre el objeto deseado.
Heat Transfer
El heat transfer también trabaja superficies planas o cilíndricas. Se trata de una especie de parche; una película de plástico transfiere su diseño a través de calor y presión a la pieza, es decir, estampa su diseño sobre el producto.
Spray masking
Por su parte, el spray masking se refiere al proceso de pintado con máscaras, es decir, cubre las partes que no se desean pintar. Con un aerógrafo se rocía pintura para decorar la parte no cubierta.
Cold runner
La serigrafía es el proceso clásico de decorado: por medio de una malla el color se imprime a presión sobre superficies planas. Así, la tinta se transfiere al producto con el diseño específico de la malla. Es una de las opciones más económicas, pero no funciona en superficies cilíndricas o irregulares.
In Mold Labeling
Otro proceso conocido como in mold labeling (etiquetado en el molde) consiste en ingresar una etiqueta en el molde del producto y encima de la etiqueta se moldea la pieza, todo esto realizado por un robot. Así la pieza tiene un acabado determinado desde el primer momento en que acaba el proceso de inyección.
Etiquetado
En otras ocasiones, el etiquetado simple es suficiente para terminar sus acabados. Consiste en pegar una calcomanía a la pieza con el diseño en lugar de pintar sobre ella.
Una vez decorado, el producto está listo, sin embargo algunas piezas requieren de un paso extra para su presentación al consumidor final.
Empaquetado
El último proceso de la línea de producción es el empaquetado o embalaje. Aunque muchos proyectos no lo requieren, el empaquetado da presentación al producto, ya sea en una caja, una bolsa, con plásticos protectores, etc.
El empaquetado de producto puede ser muy variable, pero los materiales más comunes son las cajas de cartón o las bolsas de plástico. Una vez acabado este proceso, las piezas están listas para distribuirse y llegar al consumidor final.
Ya hemos recorrido el proceso completo de fabricación de un producto de plástico. Ahora que entendemos bien cómo llega a su forma final una pieza, podemos adentrarnos en cómo puede ayudarnos la inyección de plástico a impulsar nuestro negocio.
Ideas de productos de plástico
Como bien lo dice la metodología del inbound marketing, deleitar al cliente o usuario es una de las tareas más importantes que tiene toda empresa. Si el usuario tiene una agradable experiencia de compra, o en cualquiera de las etapas previas a esta, tendremos un impacto positivo en él. Así, siempre hablará bien de nuestra empresa con sus conocidos y amigos, y atraerá prospectos más calificados que nuestros propios equipos de ventas.
¿Cómo se relaciona todo esto con la inyección de plástico? Un producto promocional, un juguete o un accesorio útil puede convertir una experiencia convencional en una sumamente agradable para el cliente. Por ejemplo, en un primer contacto en persona con el área de ventas, un obsequio útil u original puede dar una buena sensación e influir en el comportamiento de compra.
O, por ejemplo, si vendes productos en retail, un simple accesorio extra puede posicionarse por encima de tus competidores en el momento en que un posible cliente evalúa diferentes productos en su compra.
He aquí algunas ideas de lo que puedes hacer para potenciar tus ventas a través de productos de plástico.
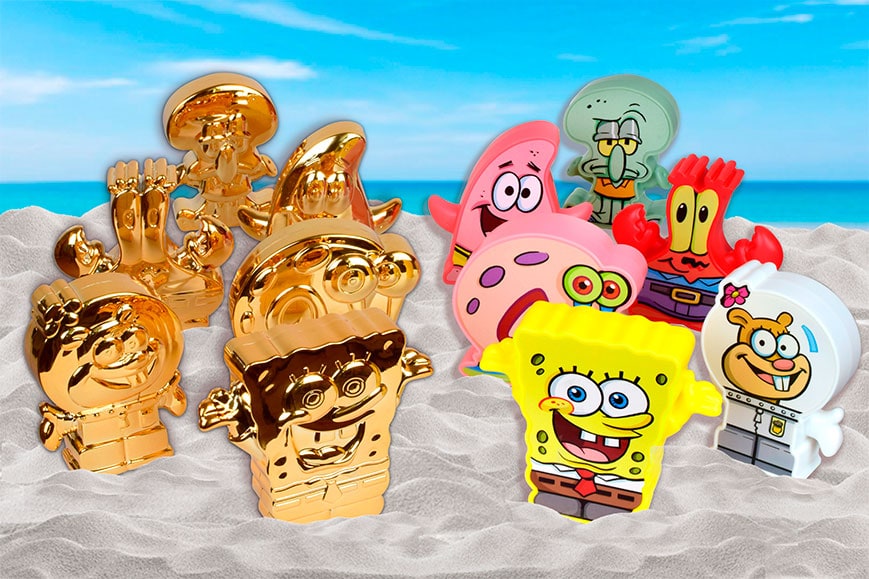
Productos promocionales de plástico
Una estrategia ya clásica del márketing es la creación de artículos promocionales. Puede tratarse de algo sencillo, como un cilindro para beber agua, una pluma o un vaso de plástico, pero también puede ser algo más creativo y elaborado relacionado íntimamente con tu negocio.
Por ejemplo, si tienes un consorcio de consultorios dentales, esas prácticas placas de plástico con una ranura al centro puede ayudar a tus pacientes a sacar el resto de la pasta dental en los envases.
Citando otro ejemplo, las cadenas de restaurantes de comida rápida, en asociación con algunas franquicias o marcas populares, suelen lanzar vasos coleccionables con estampados exclusivos. Aunque parezca una algo común, las opciones de producción suelen ser muy versátiles y siempre puedes encontrar la forma de aprotar valor al usuario con un promocional relacionado con tu producto.
Contenedores de plástico
Existen diferentes tipos de contenedores de plástico que pueden darle una ventaja a tu negocio. Los más sencillos, por ejemplo, son aquellos que se regalan junto con un producto: sandwicheras, popotes, cubiertos, botellas de agua, etc.
Los contenedores de plástico no sólo pueden estar destinados para tu consumidor final, también pueden servir de ornato para tus oficinas de venta o como un elemento útil en los escritorios de tus empleados. El impacto visual del cliente también influye en su deleite y en su decisión de compra.
Productos de plástico para el hogar
Hay una gran cantidad de productos para el hogar elaborados con plástico. Podemos clasificarlos según la sección del hogar en la que se encuentran (como hacen los centros comerciales), pero las posibilidades son muy variadas. Depende del sector de tu negocio, la campaña publicitaria que estés realizado o las necesidades que has identificado en tus clientes, estos tipos de productos pueden funcionarte mejor o peor.
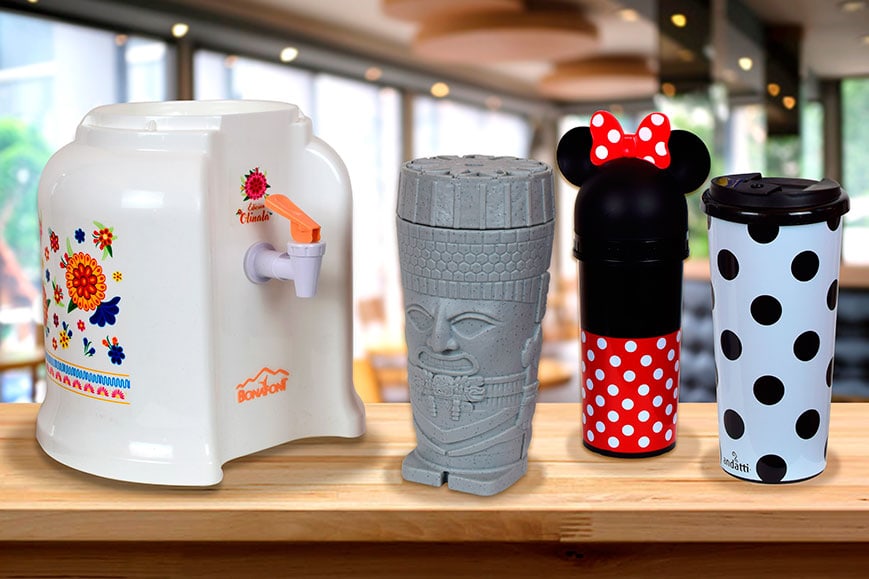
En el ámbito de la cocina tenemos muchas opciones, desde coladores, platos y vasos, hasta exprimidores, utensilios y accesorios para la mesa. La innovación de estos productos por lo general se encuentra en el diseño y la ergonomía.
El baño puede ser también un buen lugar para productos plásticos. Las jaboneras, los recipientes y los soportes para artículos de baño pueden ser muy novedosos con el equipo creativo necesario.
Incluso en el auto podemos encontrar este tipo de productos. Pueden ser artículos plásticos para tus llaves o llaveros, accesorios para el parabrisas o las ventanas, o soportes para el celular. Lo más importante aquí es la practicidad.
Juguetes de plástico
Una de los más grandes sectores de la industria plástica son los juguetes. Dentro de ellos tenemos una gran variedad según sus usos y sus potenciales usuarios. Un producto de uso lúdico siempre puede ayudarte a deleitar a tu usuario o prospecto y claro, a publicitar tu marca mientras este se usa.
Los juguetes coleccionables son todos aquellos que el cliente atesora, tienen un fin decorativo y no están hechos para jugar con ellos. Esta industria que ha ganado mucha fuerza en los últimos años. Ya sea sobre personajes, películas o videojuegos, las figuras coleccionables no se limitan al público infantil, también son ampliamente consumidos por los adultos.
En los juguetes coleccionables el proceso de decoración suele ser más complejo. La atención a los detalles de un coleccionable puede necesitar más de un proceso de decoración, ya sea spray masking, tampografía o incluso etiquetado. Están hechos para un público más exigente.

Los juguetes preescolares son cada vez más complejos hoy en día, sobre todo los que tienen componentes electrónicos. Sin embargo hay juguetes para niños muy pequeños que no tienen gran complejidad en su elaboración y pueden ser muy demandados, suelen tener métodos de producción sencillos: después del proceso de inyección de plástico necesitan poco decorado, ya sea con tampografía, con in mold labeling o con un etiquetado sencillo.
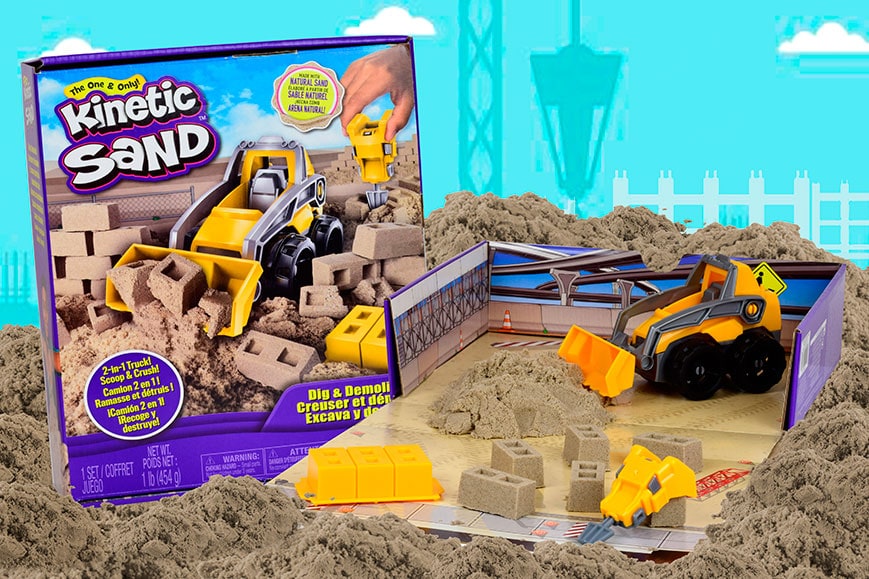
Los juegos de mesa son también muy populares y la mayoría requiere de poco material para ser elaborados. En cuanto a plástico, las fichas, los dados y los accesorios son los que pueden ser creados a la medida. Algunas marcas a lo largo de la historia han creado su propio juego de mesa para deleitar, educar y posicionar su negocio.
Los juguetes con componentes eléctricos pueden resaltar tu producto sobre otros. Claro que la fabricación de todo lo electrónico se realiza por separado y en el proceso de ensamble se une a la pieza para dar paso al producto final.
Ya hemos recorrido procesos de producción y diferentes ideas para darle un valor extra a nuestra marca o producto. Ahora una de las preguntas más importantes, ¿cuánto me va a costar esto?
¿Cuánto cuesta la inyección de plástico?
Una de las preguntas más comunes es cuánto cuesta la inyección de plástico. La pregunta es un poco complicada de responder, depende mucho del producto, del número de piezas a producir y en los procesos secundarios (ensamble, acabados y embalaje). Sin embargo, podemos determinarlo respondiendo otras preguntas más básicas:
¿Qué quieres crear?
Al identificar el tipo de producto que queremos realizar, podemos también saber en qué etapas del proceso se puede ahorrar. ¿Ya existen piezas que podamos comprar a un tercero para el proyecto? ¿Ya se han realizado diseños o productos similares? ¿El producto es viable tal y como lo quiero?
En Martin’s Plastics podemos orientarte para responder estas preguntas y así aminorar el costo de producción de tu proyecto, pero también es necesario responder otra pregunta.
¿Para cuándo lo quieres?
Si el proyecto se planea en menos de diez semanas, no se podrá producir todo desde cero, lo más viable sería buscar piezas que ya estén en circulación en el mercado,diseños ya probados o , moldes ya existentes que puedan funcionar para la pieza. Si se cuenta con más de diez semanas para su elaboración, se puede comenzar a pensar en su desarrollo desde el diseño y la elaboración del molde.
En este punto se combinan el qué y el cuándo. Si queremos un producto a la medida, con características sumamente específicas y un diseño desde cero, necesitaremos por lo menos diez semanas para la elaboración de una pieza sencilla. Si las diferenciación del producto viene en la decoración (para cilindros o contenedores, por ejemplo) se puede usar algo preexistente.
¿Cuánto producir?
El número de piezas a fabricar es uno de los factores más importantes para determinar el precio final. Debemos considerar que los moldes para la inyección suelen ser relativamente costosos. Un molde para una pieza pequeña puede costar entre 10 mil y 20 mil dólares, una de un tamaño mucho mayor puede llegar a costar 200 mil dólares.
Si, por ejemplo, piensas hacer sólo 100 piezas de un producto y el molde costó 10 mil dólares, cada pieza tendría un costo de 100 dólares sin contemplar el material necesario para producirse. Por el contrario, si tu producción será de 100 mil piezas, el costo será de 0.1 dólares sin materiales.
Normalmente se recomienda que el producto final se venda por lo menos 10 veces más caro que el costo original del molde por pieza. Es decir, si tu molde cuesta 10 mil dólares, 100 mil dólares debe ser el precio mínimo de venta total de la suma de todas tus piezas. Con esta idea puedes hacer un cálculo de en cuánto piensas vender tu producto, o qué beneficio monetario obtendrás de él, y estimar cuantas piezas necesitas producir para que sea un buen negocio.
La creación de un molde desde cero se recomienda en proyectos de al menos 100 mil dólares de venta estimados, ya que la creación del mismo molde podría no solventar los gastos del proyecto. Sin embargo, hay casos especiales en las que, sin importar el costo de producción, el cliente quiere producir pocas piezas con un molde a la medida.
Otro factor a considerar es el costo del plástico, que va desde 1 dólar por kilo hasta 6 dólares por kilo, dependiendo su calidad. Este costo sería adicional a la cotización del molde que hemos comentado.
Guía para evaluar el costo y la viabilidad de tu proyecto
Así, con la información anterior podemos hacer un presupuesto de cualquier proyecto que queramos realizar, respondiendo las siguientes preguntas:
1. ¿El proyecto es para generar ventas o para una necesidad muy específica? Si es para generar ventas, pasamos al siguiente punto. Si es una necesidad, podemos pasar directamente al punto 3. |
2. ¿El proyecto generará más de 100 mil dólares de venta? Si ese es el caso, podemos pasar al siguiente punto. Si no es así, pasamos al punto 5. |
3. ¿Cuántas piezas piensas fabricar? Aquí hay que tomar en cuenta que, en caso de que el proyecto genere ventas, debes de dividir el número de ventas totales estimadas por el número de productos a fabricar. Ese será el costo total de venta de cada producto. Una vez anotada esta cifra, pasa al siguiente punto. |
4. ¿Qué tamaño y características tiene el producto? Para aclarar los costos relacionados con la cantidad y calidad del plástico y la cotización final de un molde, es necesario acudir a un especialista. Sin embargo, con el costo total de venta de cada producto, tenemos una idea de en cuánto queremos vender nuestro producto. En relación a ello, el especialista estimará el costo de producción del producto por unidad y podrás hacer cálculos sobre el margen de ganancia. |
5. ¿Qué pasa si la fabricación de mi producto a la medida no es viable? Si en el punto anterior el costo de producción y la ganancia estimada no te deja un buen margen de utilidad, o si tu venta planea ser menor a los 100 mil dólares, existen otras opciones para ti. Un especialista puede ayudarte a encontrar alternativas más económicas a tu proyecto. |
A través de una evaluación previa de la idea, se pueden revisar opciones como encontrar una pieza ya existente en el mercado, usar moldes preexistentes o cotizar otros materiales además del plástico. El especialista le dará la solución a tu idea para que esta salga adelante, ya que él tiene las herramientas y la experiencia para ajustar tu proyecto a las posibilidades de fabricación.
En Martin’s Plastics podemos ayudarte paso a paso en la evaluación de tu proyecto. Contamos con soluciones 360, desde la conceptualización, el diseño y la producción, hasta almacenaje y distribución.
Contáctanos y resolveremos cualquier duda sobre tu proyecto.
Deja una respuesta